From engineered grades to diverse types of testing, our comprehensive value-added services ensure superior solutions for diverse steel needs.
Regardless of our customer’s industry, we’re able to satisfy their requirements thanks to our extensive experience, top-of-the-line equipment, and facilities.
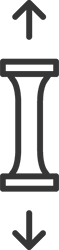
Laboratory
Mechanical, Chemical & Metallographic Testing
Our cutting-edge laboratories are equipped with the best gear to conduct mechanical, chemical, and metallographic testing.
The fully integrated Scanning Electron Microscope (SEM) and Silicon Drift Detector-Enhanced Energy Dispersive X-Ray Spectroscopy (SDD-EDX) platform addresses all micro-scale visualization needs.
Thanks to its Particle-X program, size, distribution, quantity and chemical composition of the inclusions are obtained for best process control on the steel’s cleanliness.
- Tensile, Impact & Hardness
- Hardenability
- Chemical Analysis & Positive Material Identification (Spectro)
- Micro-Cleanliness, Microstructure & Ferrite Content
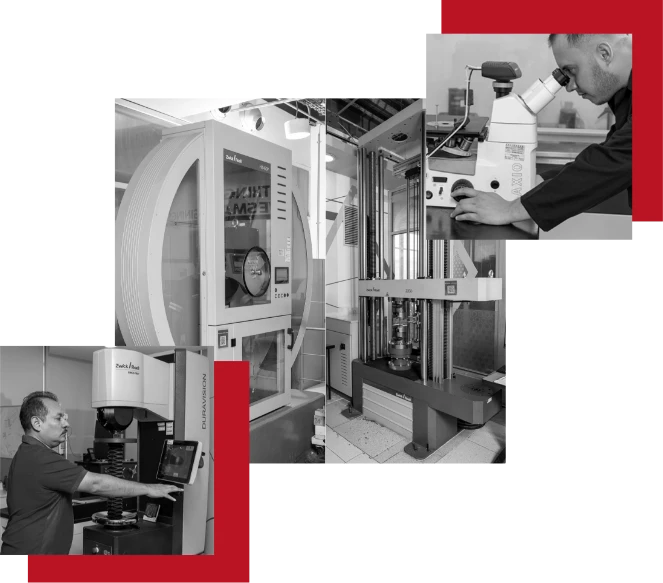
Non-Destructive Testing
The Rotating Billet
Inspection System
(RBIS)
Designed for bars >8” is a turnkey solution that uses Phased Array (PA) and Eddy Current Array (ECA) technology integrated into a fully automated testing system to meet stringent requirements for volume and surface inspections.
Inductive heat flux thermography (Defectovision)
Designed for bars <8” facilitates the testing of entire surfaces of hot-rolled steel bars with round or square cross-sections. Combined with the latest processor technology, state-of-the-art thermal imaging technology ensures that the test results are ready within seconds. Both surface and edges are examined completely, and untested ends are reduced to just a few millimeters.
The automated UT bar inspection system (Rowa)
Designed for bars <8” is engineered to meet today’s plant and end-customer quality standards while complying with all the required ultrasonic testing safety codes. Featuring automatic calibration and system checks using the Reference Standard Manipulator (RSM), this system ensures maximum calibration repeatability with no user intervention required.